As the Technical Director and Scenic Designer for this production of Grease produced by Illini Student Musicals, I had to be creative in order to efficiently use materials and labor. The scenic budget for this show was on the higher end of the scale for ISM productions at $1,200 with an 8 week build schedule and 2 day load-in.

Working with in a venue with little to no backstage space requires creativity. To accommodate the needs of this production, the orchestra was elevated 10 feet off of the deck with various areas of height on the frontside. this allowed us to create many playing spaces for the actors while allowing space to store scenery, An entire deck supports the footprint of this set as we were not allowed to screw into the stage floor. Sliding doors appear to close the open area center stage.

Figuring out how to support a raised deck holding an orchestra while allowing for scenery and actors to move underneath was challenging. We supported these longer platform spans with 4x4's horizontally across the underside.

Building offsite creates its own unique set of challenges such as transportation. For this production, we used one Penske 26' box truck for the scenery and a 16' box truck for all of the furniture. As you can see we just made things fit allowing us to make a single trip. For this productions we transported all of the scenery to the stage the night before load in so our scenery and tools would be ready and waiting.

A main focus of this production for me was Grease Lightning. Because of the 6' door opening center stage, and the means of getting a rented car through the doors of the venue, I opted into designing and building the car myself. Minus the frame with casters, the car was made from pink foam and glue. Jaxsan was used all throughout for fire proofing purposes.

The car on the left is what inspired the design of the car for our production. On the right, is the white model I created showing the use of pink foam. To achieve the rounded edges, I used spray foam on the insides of the corners to allow me to carve the corners.
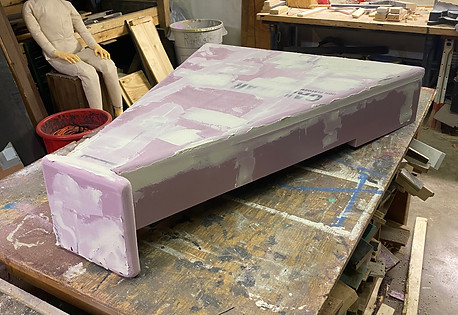
As I began to assemble the hood, I was learning quickly what techniques did work and which did not. I was trying to work quickly while maintaining a smooth surface, straight cuts, and square construction. These were all challenges as the slightest nick could damage the smoothness of the pink foam.

To build out the corners and provide strength each panel, I used a mixture of wood glue and sawdust to get the smooth curves. By spreading this about and letting it harden, I was able to use an angle grinder with a quick change grinding disk to smooth it over and shape it.

This showcases a close-to-finished product. While I wish I had gotten the surfaces a bit smoother, looking at the car from 40' was just fine and it looked great. A construction technique I am demonstrating in this image was the use of skewers to hold the foam up while the adhesive set.