Stage Machine Design Competition 2023
1st Place Overall Design and Implementation

Last year, a group of students in the Scenic Technology program at UIUC decided to team up to compete in the 2023 Stage Machine Design Competition held annually at Purdue University. The Stage Machine Design Competition is an event for students in theatre technology and engineering from various colleges and universities. The competition focuses on the mechanical design process and challenges student teams to create engineered solutions for unique stage effect challenges. The prompt for this competition says to create a life-size Guess Who panel from the childhood board game while adhering to certain guide lines. Some of the requirements focuses on the amount of travel the lever is allowed to move, the amount of input force it takes to move the lever, and that the lever has to move proportionally to the panel itself eliminating limit switches and other automated features. Winning 1st place was am awesome reward for the months of hard work and collaboration that we dedicated to this competition.

This is the main body of our system, showcasing the springs, levers, and arms used to maneuver this panel into the up position. The large garage spring in the middle acted as our main lifting force on the way up while a secondary set of springs hidden in the plywood box pulled it past center to its final position.

The panel, keyed shaft, and frame that made up the majority of the given specifications, was going to be provided at the competition. This panel was made from scrap so we could test and tune our components. The panel weighed roughly 30lbs, and was even lighter on competition day.

This large gray box initially acted as the control hub with sets of gear reductions inside to allow for minimal forces to be applied to its handle. Another feature of this design is the use of a worm gear acting a safety break preventing the panel from driving the lever and hurting the user. These components were ultimetly removed as the 3D printed gears could not handle the force required.

Acrylic played a major role in our design. Because we had some 1/2" acrylic in stock and I was feeling creative, I decided to make these two levers out of it using our Shopbot CNC. This allowed us to make new connections and positions without compromising the integrity of the material because of its durability. The acrylic performed just fine and looked good at the same time.

This image shows an initial design of the lower frame. It incorporated components we knew we needed such as framing to bolt to, levers to create mechanical advantage, lever arms, sprockets, and keyed shafts among other things. This design evolved constantly in CAD, but even more so as we began to fabricate and test.
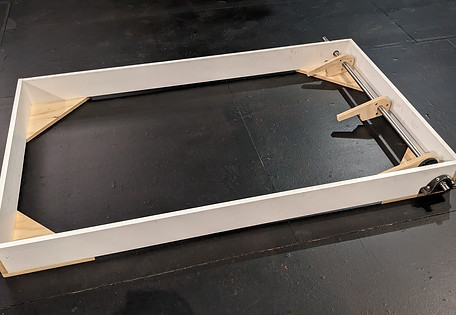
This is the panel that was provided at the competition. Note that the plywood panel is missing from the center because a team after us drove the panel too fast and broke the sleeves. I included this photo because of how the plywood corner blocks are attached to the underside of the frame. This lifted the shaft 3/4" higher than in the provided design. We quickly brainstormed and were able to raise our entire frame to the new height using scrap material and the judges awarded us extra time for the mistake on their end.